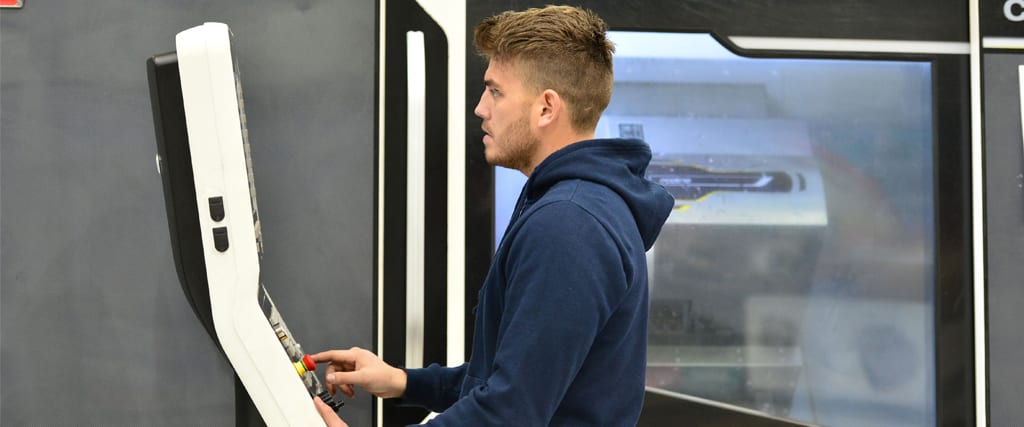
HP10 CNC-Turning / CNC-Drehen
CNC turning could be for you if you like:
- Making things
- Solving complex problems
- Using tools
- Using computers
More about this skill:
CNC Machining has become one of the most important and present machining processes in modern industry. Parts are made for household-equipment, tele-communication, cars, ships, aeroplanes, oil rigs, bridges, aerospace etc. Customers come from virtually every branch. In CNC Machining the movements of the machine through computers and servomotors are dictated by the programmer. Once correctly programmed and set up, these machines can produce almost any shape and can repeat the process (big advantage) many times.
CNC Machining covers a broad variety of machining processes, such as grinding, welding, electrical discharging, milling … and also turning.
Some may think that Lathe’s (turning machines) are built to make round parts the CNC lathe’s are capable of producing almost any shape and any part. Every customer has different requirements and demands and therefore each part is made of different materials, needs different geometries, dimensions and surface qualities. To explain all the desired requirements to the machinist, the customer produces a technical drawing.
Where does CNC machining start with? First the best way how to produce the part has to be decided. There are many ways of doing this, like welding, milling, casting, and 3D Printing. One very important method is CNC-Turning. A CNC lathe is a very accurate computer-driven machine, where cutting tools, controlled by a program, are moved to cut away excessive material to result in the expected customer part. The CNC-Turning machinist receives the technical drawing and uses the lathe in many ways to find solutions to build the part. These machines are very expensive, because they can do remarkable things. To have an idea of this, think what it means to achieve accuracy below ten microns, which
is six to 10 times thinner than a human hair.
The CNC-Turning machinist uses a computer to tell the lathe how to move the tools and cut the part to the desired shape. He/she also must set up the lathe with all the clamping devices, support devices, and cutting tools. These tools can cut almost every material (stainless steel, plastic, soft steel, aluminium, bronze, and so on). But he/she has to choose well to avoid temperature variations, tool wear or vibration. Those things influence the product and it can result in poor quality. When the machine starts cutting material, the machinist makes sure that the dimensions exactly fit the customer specifications. For this, very accurate inspection tools are used.
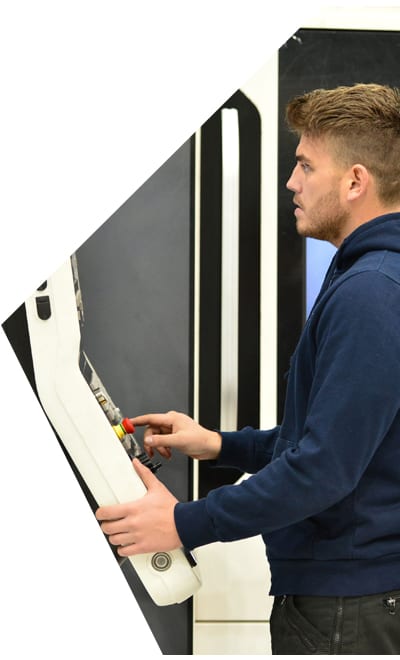